Compliance Testing
With over 13 years experience in completing these services, electrical compliance testing services form part of Tagteam’s core service offering.
Tagteam can manage the following electrical compliance testing services:
- Appliance test and tagging
- RCD switchboard testing
- Emergency and exit light testing
- Thermal imaging
- Switchboard maintenance
- Co2 calibrations
- Microwave leakage testing
- Generator inspection
- Power factor correction
- Lux level testing
And our qualified electricians can replace or repair your failed items on site, to save you further in call out fees and lost time.
All of these services, including due dates and certification information are all managed through Valid8, Tagteam’s purpose built electronic job management system.
Tagteam’s electrical compliance testing is often combined with essential services required for fire equipment and HVAC – call our office now to discuss a comprehensive solution for your business.
Appliance Test And Tag
Every business in Australia and New Zealand is subject to regulations regarding electrical testing and compliance including appliance testing and tagging. It is critical for businesses to meet the requirements of AS/NZS 3760:2010 In-service safety inspection and testing of electrical equipment and the WHS Act 2011. Fines of up to $28,500 or imprisonment, depending on the degree of seriousness apply to organisations and individuals who do not comply with these standards and legislation. But the importance of testing and tagging is far more serious than fines. Failure to complete your electrical test and tag could result in damage to your equipment and premises, fire and the risk of of electrical shock or serious injury to your staff and clients. Needless to say, appliance test and tagging is a vital task in ensuring your business will
- Remain compliant
- Secure your assets
- Protect your people
- When it comes to electricity, you simply can’t afford to take any chances.
Fortunately, the solution is much easier than the consequences. All it takes is one phone call and Tagteam’s experienced, qualified technicians will attend to inspect your electrical systems and appliance complete the required compliance testing.
Our electricians are licensed and can repair or replace your failed items while on site to minimize further disruptions and down-time for your business.
In addition to simple test and tag safety procedures, Tagteam can implement a complete solution designed for your business. We can combine multiple services at thousands of sites across Australia and provide you with the surety that every premises in your portfolio is compliant. And Tagteam’s purpose-built Valid8 system means you will never have to worry about consistency again., all results and Compliance Certificates are accessible online instantly.
RCD Testing
Residual Current Devices (RCDs) are electrical safety switches designed to prevent fatalities. When a faulty appliance is plugged into your electrical system, or when a person accidentally touches an energized piece of equipment, it’s critical that the electrical supply is cut off in an instant. RCDs save lives every year, but like all types of electrical equipment, they’re prone to wear and tear. When an RCD device is no longer functioning at full capacity, the stakes are high. One wrong step could mean electrocution.
Tagteam will keep your business compliant and safe by completing your RCD testing and replacing any failed devices on site. This testing is required under the WHS Act 2011 and AS/NZS 3760 which recommend Push Button Testing every 6 months and Time Testing annually. Tagteam’s technicians are experienced, qualified electricians who can replace any failed RCDs while on site, an important part of our testing solutions when you consider the impact of failed RCD.
Failed RCDs can result in extensive downtime, disruptions to your normal operations and costly replacement and call-out fees as well as placing unnecessary risks to the safety of your staff. We will schedule your RCD testing through our Valid8 system to ensure you don’t need to worry about due dates and compliance again. This testing can be packaged with our comprehensive maintenance solutions to save your business time and money.
Emergency And Exit Light Testing
The confidence to pass any regulatory inspection or work health safety audit.
Tagteam employs only the best electricians to test, repairs and maintain your emergency exit lighting systems so that you can ensure your business is protected and fully compliant with AS/NZS 2293:2005 Emergency escape lighting and exit signs for buildings at all times.
This regulation requires that all emergency and exit light fittings be maintained and subjected to a thorough inspection every six months. The 90 minute discharge test is to ensure that in the event of an emergency, your exit lighting fixtures will be functional and allow all occupants to exit to safety.
Should any items fail our testing, Tagteam electricians are qualified to make any needed repairs on-site. Our electricians carry LED fittings that offer a significantly longer life span and more effective lighting than traditional fluorescent fittings.
Our emergency exit light testing program is scheduled with other essential services such as fixed and portable fire protection equipment to align with your annual fire safety statement (AFSS) due dates and offer you the value of a comprehensive maintenance package.
Thermal Imaging
magine you get a call from your staff one morning… one of your electrical switchboards has caught fire. Your pulse starts racing. Which one was it?
Which one do you hope it’s not?
If you run a restaurant, what’s going to happen if one of your freezers or refrigeration units suddenly stops receiving power? How much is it going to cost to replace all your lost stock?
If you rely on data servers, what’s going to happen to your business if there’s an electrical fire that destroys one of your hard drives? How much is it going to cost to recover?
What if you could keep that money in your pocket, save money on insurance premiums, and save time?
With thermal imaging, or Thermography, our expert technicians can find future problem areas that are invisible to the naked eye.
magine you get a call from your staff one morning… one of your electrical switchboards has caught fire. Your pulse starts racing. Which one was it?
Which one do you hope it’s not?
If you run a restaurant, what’s going to happen if one of your freezers or refrigeration units suddenly stops receiving power? How much is it going to cost to replace all your lost stock?
If you rely on data servers, what’s going to happen to your business if there’s an electrical fire that destroys one of your hard drives? How much is it going to cost to recover?
What if you could keep that money in your pocket, save money on insurance premiums, and save time?
With thermal imaging, or Thermography, our expert technicians can find future problem areas that are invisible to the naked eye.
Here’s how it works:
Before switchboards and other electrical equipment fails, it begins to slowly deteriorate. As it deteriorates, it produces heat, or “hot spots.” These hot spots cannot be seen in visible light, but they can be seen using an infrared camera.
By using highly sensitive thermal imaging equipment, our team can pinpoint these anomalies before they fail and cause damage to your assets, or even worse: start a fire.
When you call Tagteam to schedule your thermal imaging appointment, we’ll send our qualified, highly skilled electricians to your property with our latest cutting edge thermal imagers to spot problems before they become a hazard to you, your business, and your people.
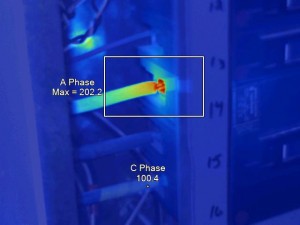
We can use our sophisticated Thermography techniques to inspect for hot spots on a range of equipment types, including:
- Switchboards
- Control Panels
- Distribution Boards
- Mechanical Switchboards
- Main Switchboards
When you schedule your thermal imaging inspection for you business, you’ll also want to check with your insurance company to ask if they’re one of the many providers who offer a discount on their insurance premiums for companies that engage in proactive maintenance inspections, such as Thermography.
All thermographic scans are carried out by Tagteam with consideration to AS 3000: Electrical installations and are performed at a peak load time by our qualified A Grade electricians and detailed reports are available through the Valid8 system.
Switchboard Maintenance
Tagteam conduct switchboard maintenance as part of routine maintenance so ensure your electrical switchboards are operating at peak condition.
This maintenance includes the following for each switchboard:
- Internal and external cleaning, including dusting and removal of rubbish and debris
- Checking of cabinets, doors, gaskets, glands and cable entries to ensure the integrity of segregation between compartments
- Inspecting all penetrations and cable entries to ensure they are sealed and safe from dust and vermin
- Checking temperature probes and smoke detectors
- Ensure all legends are available, correct and secured in the switchboard
This simple inspection and maintenance is completed by our licensed electricians to protect your assets and electrical systems.
Co2 Calibrations
All beverage dispensing machines that store Co2 need to be constantly monitored to ensure gas is not leaking from the system. A popular and effective option is the use of a Co2 monitor which will alarm when gas is detected.
Co2 monitors and their sensors should be calibrated and maintained every 6 months in accordance with the manufacturers instructions and warnings, as well as AS/NZS 60079: Electrical apparatus for explosive gas atmospheres and AS 2865: Confined spaces.
Tagteam can assist with the supply and installation of Co2 Monitors as well as on-going calibrations and maintenance. The 6 monthly inspections are combined with Tagteam’s other 6 monthly services, such as RCD testing, emergency and exit light testing and portable fire equipment inspections to offer value to clients in comprehensive maintenance packages.
With clients in pubs, clubs, bars, hotels, convenience stores and petrol stations across Australia, Tagteam are an experienced, preferred supplier of Co2 monitor calibrations and inspections.
Microwave Leakage testing
Microwaves use radiation to heat up your food. When functioning properly, this radiation is contained within the microwave.
The problem comes when over time the microwave is no longer able to contain the radiation to inside the device while it’s operating. This allows dangerous high-frequency electromagnetic wavelengths to seep out and into the break room and surrounding workplace.AS/NZS 60335.2.25 and AS/NZS 3760 requires that the radiation leaking from workplace microwaves be kept below certain limits at all times. It’s recommended that employers have their workplace microwaves inspected every 12 months so that any problem areas can be corrected, preventing dangerous radiation from permeating your business.
Tagteam technicians are able to inspect your microwaves along with other routine maintenance calls to keep your costs down and your people safe.